Rapidly growing custom metal forming company Roller Die recently purchased the assets of Redall Industries, a roll forming facility located in Yale, Michigan. 12/30/24 Â – Roller Die + Forming recently completed an asset purchase from Redall Industries, located in Yale, Michigan. This existing roll form facility has a number of advanced manufacturing technologies and will […]
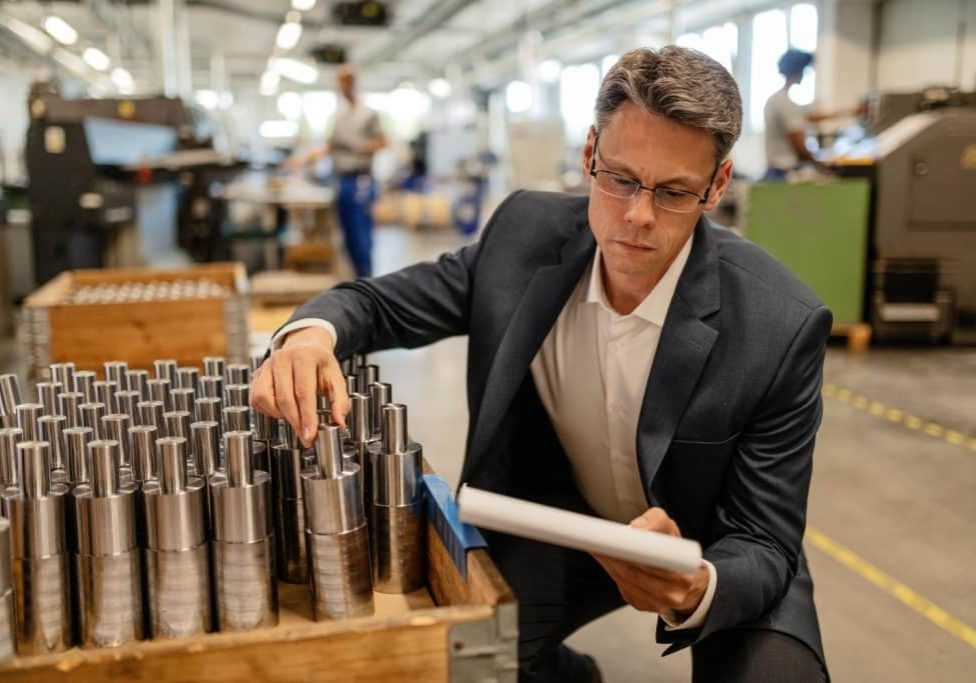
How Steel Market Trends in 2025 Will Impact Manufacturers
As we look toward 2025, the steel market is poised for substantial transformation, bringing both challenges and opportunities for manufacturers. With rapidly advancing technologies and shifting consumer demands, the industry is evolving at an unprecedented pace. These changes are crucial for manufacturers to understand to stay competitive and efficient. The increasing emphasis on sustainability is […]
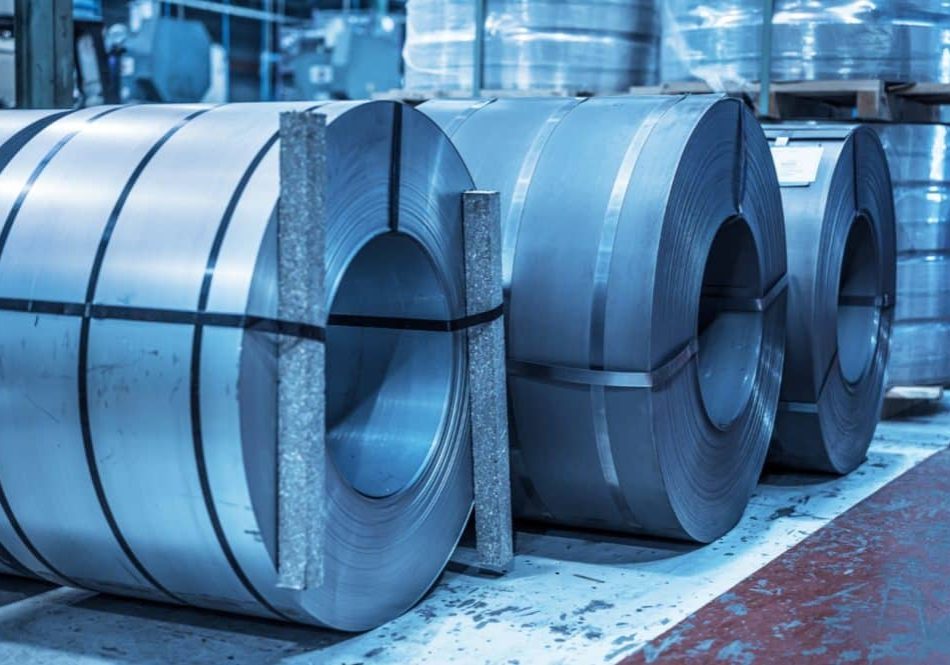
Why Roll Forming is Great for Manufacturers
Roll forming is a process that transforms metal into specific shapes using a series of rollers. This method creates products that are precise and consistent, making it vital for many industries. Manufacturers are increasingly turning to roll forming due to the numerous advantages it offers over other metalworking techniques. One key reason manufacturers favor roll […]
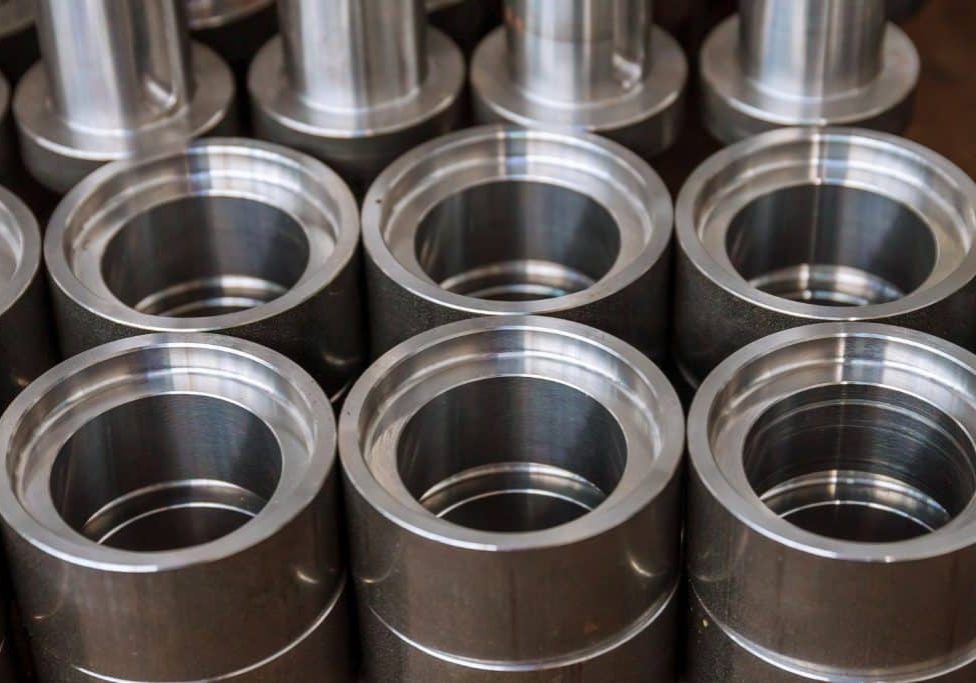
Discover the Smart Ways to Use Custom Roll Formed Parts
Custom roll formed parts offer incredible benefits for a variety of industries. From automotive to construction, these parts provide strength, precision, and cost savings. Roll forming is a continuous bending operation, allowing for high-volume production of complex shapes with high dimensional accuracy. This process can handle both ferrous and non-ferrous metals, making it versatile for […]
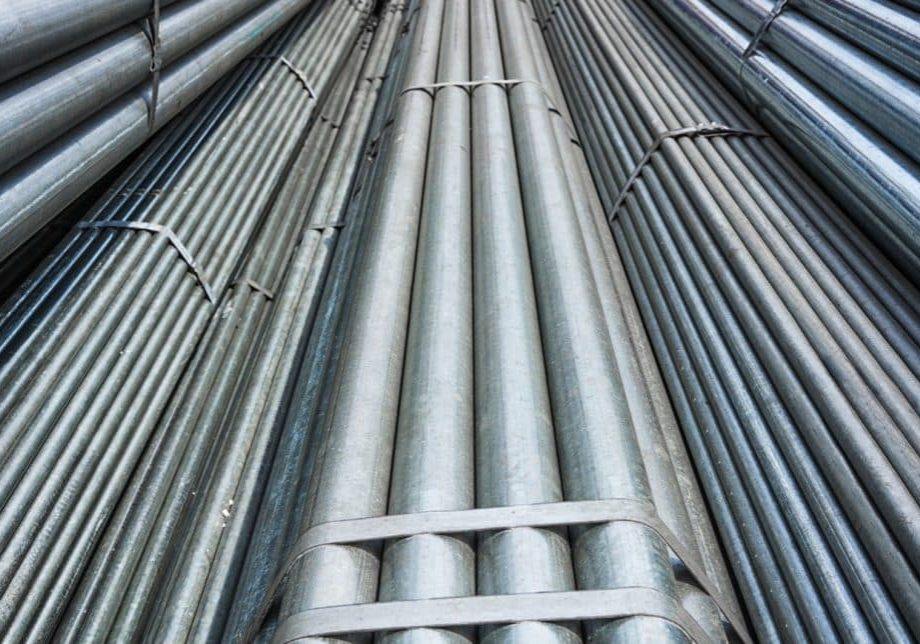
Easy Tips for Managing Metal Supply Chains
Managing metal supply chains can be a complex task, but with the right strategies, it becomes much easier. A well-organized supply chain is crucial for manufacturers who rely on metals like steel and aluminum. These materials are essential for various applications, and any hiccups in the supply process can cause significant delays and increased costs. […]
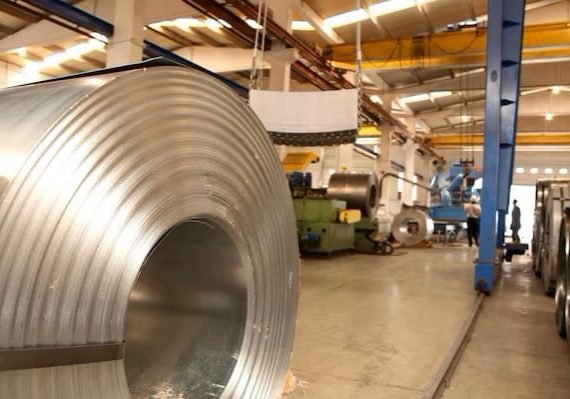
Exciting New Roll Forming Tech for Manufacturers
Manufacturing is evolving, and so is roll forming technology. For those in the industry, staying updated with the latest advancements is essential. These innovations not only improve efficiency but also enhance product quality. Today’s roll forming machinery and techniques are more advanced than ever, offering manufacturers a range of benefits. From automated machines to real-time […]

Best Practices for Custom Roll Formed Products
Custom roll forming is a specialized process that shapes metal strips into specific profiles using continuous bending operations. This method is highly efficient for producing large quantities of consistent and precise metal parts. It is widely used in various industries including automotive, construction, and electronics due to its versatility and cost-effectiveness. Understanding the ins and […]

Why Recycled Metals Matter in Manufacturing
Recycling metals is transforming the manufacturing industry. Many manufacturers find that using recycled metals offers numerous benefits beyond cost savings. From environmental advantages to quality performance, recycled metals are essential in various sectors. Understanding these benefits is crucial for manufacturers looking to stay competitive and sustainable in 2025. Benefits of Using Recycled Metals in Manufacturing […]
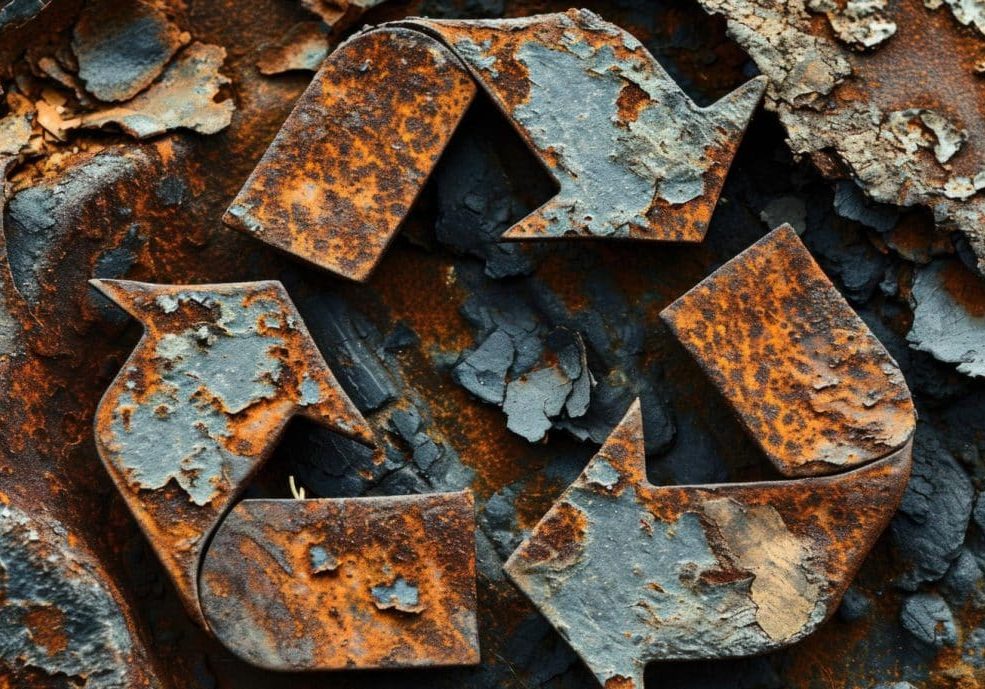
Why Recycled Metals Matter in Manufacturing
Recycling metals is transforming the manufacturing industry. Many manufacturers find that using recycled metals offers numerous benefits beyond cost savings. From environmental advantages to quality performance, recycled metals are essential in various sectors. Understanding these benefits is crucial for manufacturers looking to stay competitive and sustainable in 2025. Benefits of Using Recycled Metals in Manufacturing […]
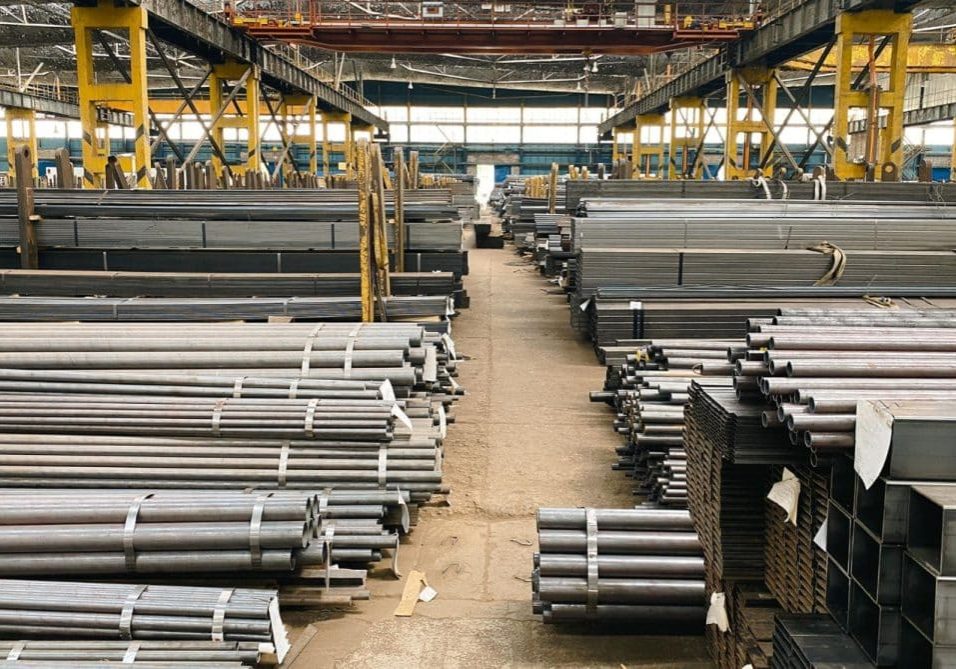
2025 Forecast: Trends and Predictions for Steel & Metal Markets
The steel and metal markets are set for an exciting year in 2025. Various factors will shape these markets, impacting everything from production methods to pricing. Manufacturers must stay informed to navigate these changes effectively. Understanding global economic influences, technological advancements, and regulatory changes is crucial for staying competitive. Technological innovations are playing a huge […]
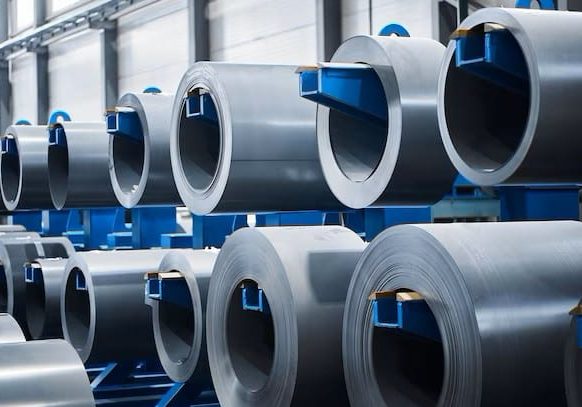
Top Tips for Using Custom Roll Formed Products
Custom roll forming is a powerful manufacturing process that transforms metal strips into desired shapes with high precision. This technique allows manufacturers to create unique and specialized parts tailored to their needs. Whether you’re in construction, automotive, or electronics, custom roll formed products can significantly enhance your production capabilities. Understanding the basics and the benefits […]
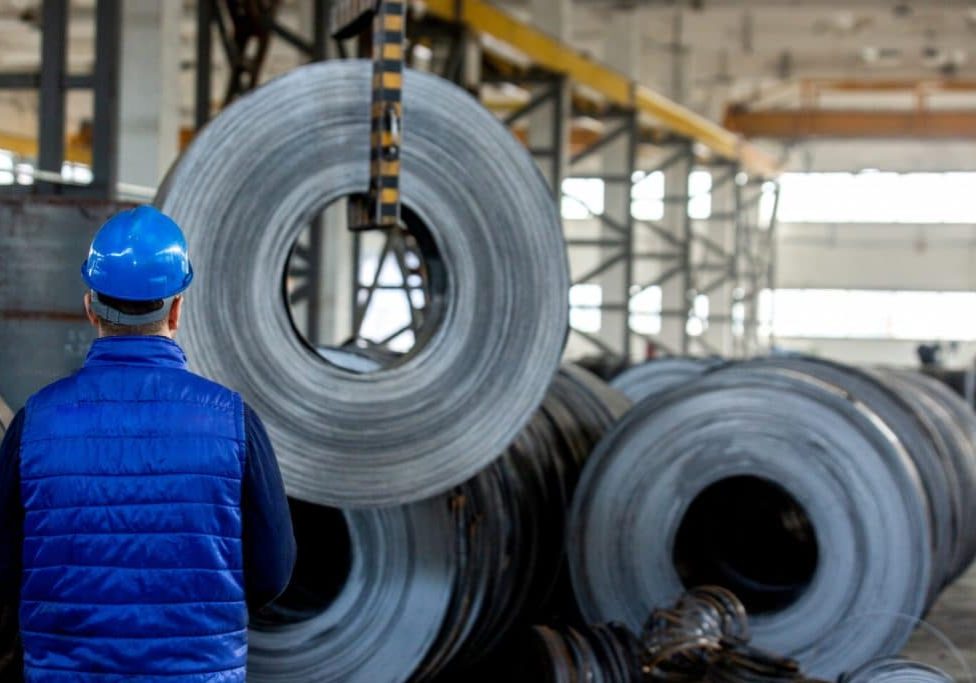
Key Steel Market Changes Manufacturers Should Watch in 2025
2025 is shaping up to be an eventful year for the steel industry. As manufacturers, keeping up with market changes is crucial. This year brings a mix of global demand shifts, economic challenges, and technological advancements, all of which will impact steel production and pricing. One major factor to watch is the demand for steel […]